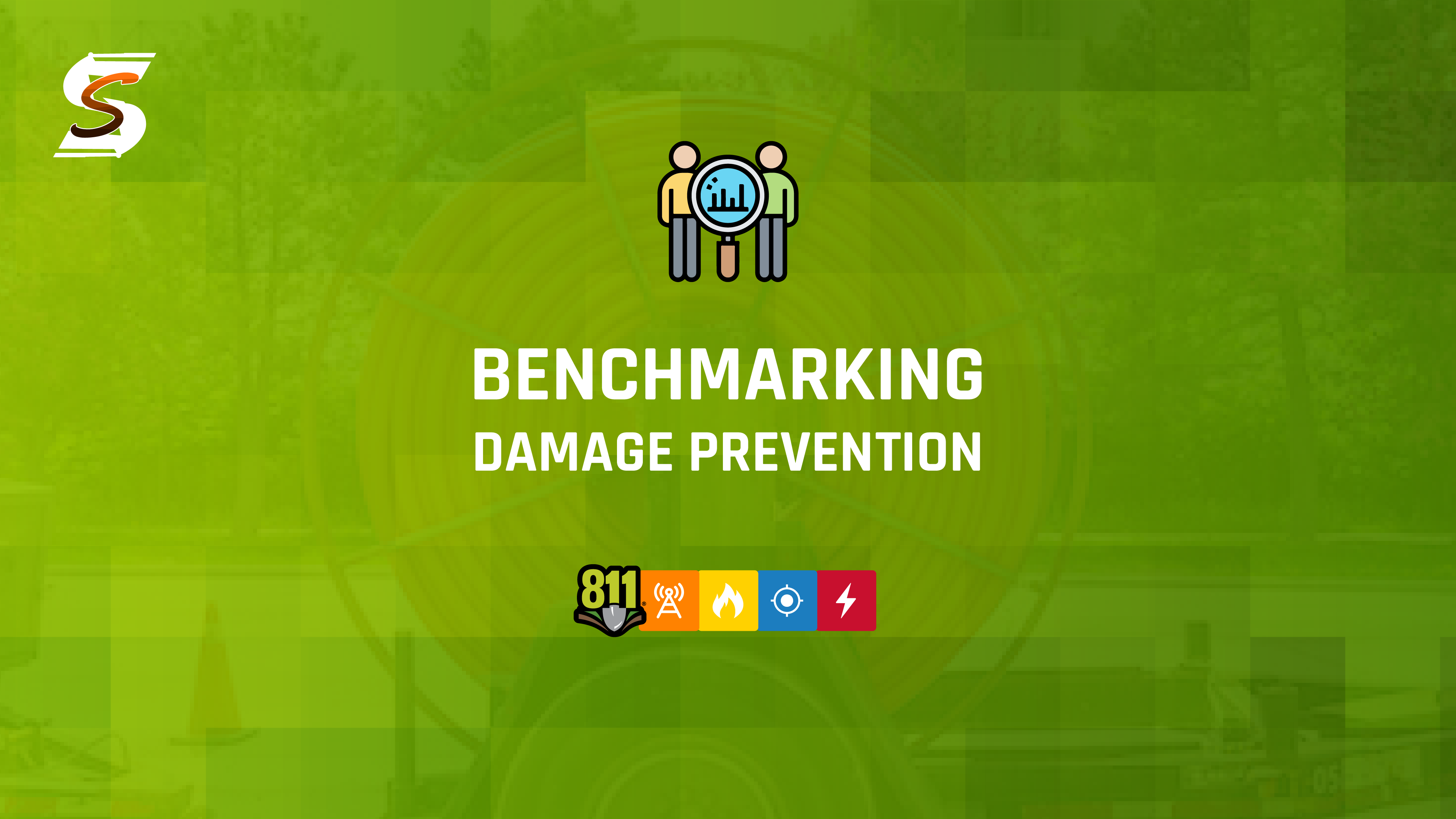
The Common Ground Alliance (CGA) provides an invaluable service annually by compiling comprehensive data through its DIRT Report and the Damage Prevention Institute. It would be beneficial to dive deeper into this data, alongside additional information from the broader damage prevention landscape. While safely working around buried utilities is a universal challenge, some industries have been more effective than others at preventing dangerous and costly excavation damages. By analyzing damage data, prevention programs, and best practices across different utility sectors, we can gain insights to improve performance and mitigate risk. This exploration will enable us to construct a more holistic understanding, allowing for a comparative analysis of how various utility industries approach and manage damage prevention strategies.
Fiber / Telecom Industry
The telecom industry, with millions of miles of buried cable and fiber lines, is no stranger to third-party excavation damage. According to the 2022 DIRT Report, there were 82,628 reported unique damages, with 50% having the root cause not listed. 11% of damages were due to locator error, while another 11% occurred because no notification was made to 811 before digging.
This damage rate has remained stubbornly high over the past decade, despite telecom companies investing heavily in robust damage prevention processes like detailed locating and marking, cloud-based location management systems, and excavator education programs. Backhoes were the most common equipment involved, striking telecom lines over 23,000 times, with Florida being the state with the highest number of incidents.
While the massive fiber expansion driven by the infrastructure bill is promising for bridging the digital divide, the widespread use of horizontal directional drilling (HDD) for installation poses risks that must be addressed. Although HDD is generally safer than open-cut excavation, the drill paths can still intersect and damage existing underground utilities like telecommunication lines, pipelines, and electrical cables.
Many contractors bypass notifying 811 before HDD operations under the assumption it is unnecessary for this trenchless technique. However, failing to have utilities properly located and marked beforehand can lead to service disruptions, environmental impacts, and potential safety hazards.
It is crucial for the industry to increase education on calling 811 for all excavation and drilling activities, even trenchless methods like HDD which are inherently lower-risk but not risk-free. Enforcement, collaboration between stakeholders, and ensuring accurate utility mapping and locating are also critical for safe and responsible fiber deployment using HDD amid this historic infrastructure initiative.
Oil & Gas Pipelines
According to PHMSA data the average direct cost of an excavator damage to a pipeline is $640,645, the most expensive excavator damage in the last 14 years cost $35,040,078. Oil and Gas pipelines are both dangerous and expensive.
Excavation damage is consistently one of the leading causes of pipeline incidents for oil and gas operators. Since 2010 there have been 855 excavator caused damages to pipelines which is an average of around 61/year. But the potential consequences extend far beyond financial impacts. Pipeline strikes can cause catastrophic ruptures, fires, environmental damage, injuries and loss of life in worst-case scenarios. This high-stakes risk underscores the criticality of damage prevention for this sector.
Regulatory-driven integrity management programs that incorporate Public Awareness, One Call participation and line locating have been instrumental in raising the priority level of damage prevention at pipeline companies.
One distinguishing aspect of Oil & Gas Pipelines from other utilities is their commitment to publishing some of their mapping data. The National Pipeline Mapping System (NPMS) Public Viewer allows users to view NPMS pipeline, liquefied natural gas (LNG) plant, and breakout tank data for a specific county or offshore area. This includes access to attributes and pipeline operator contact information. Additionally, the Public Viewer enables users to view gas transmission and hazardous liquid pipeline accidents and incidents dating back to 2002 across the entire United States. It is important to note that the NPMS pipeline data encompasses gas transmission pipelines and hazardous liquid pipelines under PHMSA's jurisdiction. However, it does not include gas gathering or distribution pipelines, such as lines delivering gas to residential customers. Consequently, not all pipelines within an area will be visible in the Public Viewer. This level of transparency from Oil & Gas Pipeline operators in sharing their mapping data should serve as an exemplary model for other utility owners to emulate and promote greater openness.
Oil & Gas operators also do more routine monitoring of their infrastructure including aerial surveys.This includes conducting regular aerial surveys to identify potential issues or encroachments along their pipeline rights-of-way. Aerial patrols, either by helicopter or drone, allow operators to visually inspect large areas relatively quickly. These aerial assessments complement other monitoring techniques like in-line inspection tools and ground-based leak surveys. The combination of mapping data accessibility and proactive monitoring demonstrates the Oil & Gas industry's commitment to pipeline safety and damage prevention.
This level of transparency and vigilance from Oil & Gas Pipeline operators in sharing mapping data and monitoring infrastructure should serve as an exemplary model for other utility owners to emulate and promote greater openness and protection of vital assets.
Electric Utilities
While less dramatic than pipeline ruptures, damages to electric distribution and transmission networks wreak havoc in the form of widespread outages, public disruption, costly repairs and absorbed claims. According to the 2022 DIRT Report, there were 17,637 reported unique damages to electric utilities, with the leading cause not listed. The second leading cause was due to locator error. Backhoes were the most common equipment involved in electric utility damages, followed by "unknown" equipment type. Contractors were most likely to damage electric lines compared to other groups.
As electricity demand grows and urban areas expand, utilities face challenges maintaining infrastructure and preventing damage from digging, natural disasters, and equipment failures. A significant trend is undergrounding power lines, which reduces exposure to weather, improves aesthetics, and lowers accidental damage risk, albeit with higher upfront and maintenance costs.
Another notable development is electric companies bringing utility locating services in-house, particularly in high-risk areas. Locating precisely identifies underground infrastructure before excavation to prevent accidental damage during digging that can cause outages, repairs, and safety hazards. In-house locating allows greater control, efficiency, prioritization of requests, and leveraging deep infrastructure knowledge for improved accuracy. It also enables better coordination with utility maintenance and repair teams.
Overall, undergrounding and in-house locating are key trends driving damage prevention improvements in electric utilities, reflecting their commitment to innovative solutions that mitigate risks and ensure reliable power supply.
Water & Sewer Utilities
In arid regions like Arizona and the American Southwest, water scarcity has become a paramount issue for water and sewer utilities. The convergence of population growth, climate change, and limited water resources has compelled these utilities to intensify monitoring and damage prevention efforts to achieve sustainable water management amid challenges like leaks and system failures.
To combat scarcity, utilities are deploying comprehensive monitoring systems that accurately track water usage, detect leaks, and identify distribution network inefficiencies. Advanced technologies such as smart meters, remote sensors, and data analytics platforms enable real-time monitoring of water flow, pressure levels, and consumption patterns. These insights allow optimization of water distribution, proactive leak/abnormality identification and remediation before escalation.
In water-scarce Arizona, damage prevention is vital. Water pipeline leaks result in significant losses, infrastructure deterioration, service disruptions, and increased operational costs. Proactive strategies like regular inspections, leak detection tech, and asset management programs minimize water loss, extend infrastructure lifespan, and improve overall system reliability.
Additionally, these damage prevention efforts protect water quality by reducing contamination risks and preserving vulnerable ecosystems in water-scarce areas. Preventing leaks and spills safeguards environmental integrity.
By integrating advanced monitoring tech and data-driven approaches, water utilities can enhance operational efficiency, optimize resource allocation, and rapidly respond to droughts, supply fluctuations, and infrastructure vulnerabilities. Leveraging these tools while focusing on damage prevention allows utilities to promote sustainable practices and ensure reliable clean water access for communities in water-stressed regions like the Southwest.
To drive improvement, some of the leading water/sewer providers are consolidating their geographic information system (GIS) data, investing in GPS tools for locating crews, mandating utility location verification through vacuum excavation on major projects, and exploring emerging technologies like subsurface utility mapping.
Others are exploring strategies like expanding reporting processes to capture more root cause data on damages, conducting outreach campaigns to high-risk excavation groups like homeowners and plumbers, or reorganizing damage prevention roles into centralized programs.
Overall, the water/sewer industry recognizes that managing safety around buried assets is critical for avoiding outages, environmental incidents, and unnecessary costs.
Cross-Industry Best Practices
While the specifics vary across telecom, pipelines and electric utilities, the organizations driving top-tier damage prevention results share some commonalities:
- Stringent performance monitoring metrics tied to incentives/penalties
- Dedicated prevention programs and management personnel
- Share more mapping
- DIRT Report Integration and DPI participation (ask Sam Hall )
- Systematic processes for investigating incidents and applying lessons learned
- Proactive public awareness, excavator education and enforcement initiatives
- Partnerships with one-call centers, regulators, and industry groups to share best practices
- Adoption of damage prevention technologies like Utilocate
At the end of the day, world-class damage prevention hinges on committed leadership, programmatic rigor, flawless execution of best practices, and a relentless focus on continuous improvement through constant measurement.
Share this Post